- Published on
Podcast Recap: Inside the Rotary-vs-Linear Actuator Showdown Shaping Humanoid Robots
- Authors
- Name
- Humanoids daily
- @humanoidsdaily
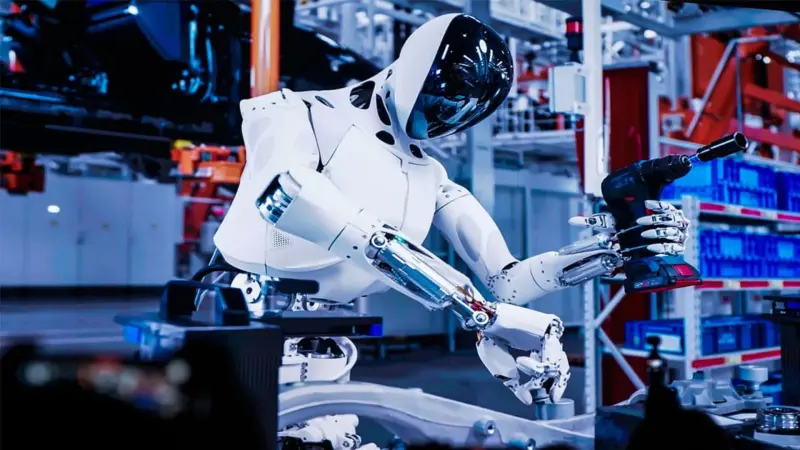
A debate that defines the hardware stack
In the latest Soft Robotics Podcast episode — “The Great Rotary vs. Linear Debate: Who Will Win?” — host Marwa ElDiwiny speaks with veteran robot-design engineer Scott Walter about one of the most consequential choices in humanoid hardware: whether to drive joints with rotary actuators or with linear actuators built around planetary-roller screws (PRS). Their 87-minute conversation lays out the technical trade-offs, the historical context, and what each path means for simulation and supply chains.
Why actuators matter
The bulk of the cost of a humanoid will be in actuators.
Humanoid robots need compact, high-torque, low-backlash joints that can survive millions of cycles. Rotary drives place a motor (often with a harmonic or planetary reducer) directly at the joint. Linear drives convert motor rotation into push-pull motion via a screw, then use linkages to swing the limb.
- Efficiency & simplicity. Rotary systems avoid the double conversion (rotation → translation → rotation) that linear linkages introduce, preserving torque and reducing parts.
- Packaging advantages. Linear cylinders can tuck powerful motors into the thigh or forearm, slimming high-torque joints such as knees, ankles, and wrists.
- Simulation burden. Complex linkages are harder to model accurately. “Simulation used to be an afterthought. Now it has to be part of your hardware design process. If your robot doesn’t simulate well, you can kiss RL goodbye,” Walter warned.
- Supply-chain wild card. Precision roller screws are expensive and made by only a handful of firms; shortages could bottleneck large-scale production.
It seems silly to convert rotational motion into linear motion only to convert back to rotation.
Two camps, one hybrid middle
Walter maps today’s players onto a “geopolitical” actuator map:
Camp | Representative companies | Dominant strategy |
---|---|---|
North Pole | Figure AI, Boston Dynamics, Agility Robotics, 1X, many Chinese startups | All-rotary |
South Pole | Apptronik (Apollo), XPeng Robotics (Iron) | Mostly linear, some rotary |
Equator (Hybrid) | Tesla (Optimus), Neura Robotics (4NE-1) | Mix of rotary & linear |
If you want to guarantee that your bot won’t be fast, then you have linear actuators.
Rotary-only bots are currently the fastest movers: no robot with PRS-driven legs has yet walked faster than ~1 mph in public demos, according to Walter.
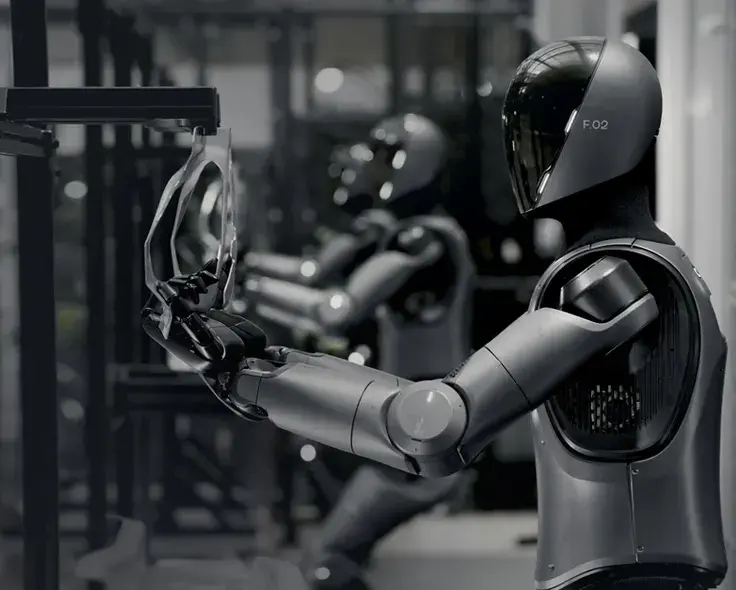
Torque curves, dead-locks and durability
Walter illustrated how three- or four-bar linkages driven by a screw can “dead-lock” at the extremes of travel, starving the joint of torque and limiting range to ~135 ° in practice. Rotary joints, by contrast, deliver a near-linear torque curve across their full range.
Durability is still an open question. Compact rotary drives must handle off-axis loads directly on the rotor, while remote linear drives keep side-loads in the linkage — a trade-off that could influence mean-time-between-failure once field data arrives.
How this ties back to the roller-screw controversy
Last month a Fast Company story framed planetary-roller screws as the “tiny screws powering the humanoid revolution,” claiming they’re used by Figure AI, Agility and others. That prompted Figure AI CEO Brett Adcock to dispute the claim, noting his robots are all-rotary. We covered the dust-up and you can revisit that analysis here.
Walter’s podcast comments clarify why the misunderstanding arose: only companies that commit to linear cylinders actually need PRS, and right now they are the minority.
Where the jury stands today
- Momentum favors rotary. Faster locomotion results, simpler simulation workflows, and an abundant BLDC-motor supply chain all tilt the market north.
- But linear keeps niche advantages. For ultra-slender wrists or tightly packaged knees, a remote linear drive can still win on geometry.
- Expect hybrids. Walter predicts many developers will reserve PRS-based drives for the handful of joints where they buy decisive space or torque — if component costs fall.
As actuator designs improve, rotary actuators will likely dominate the landscape.
Catch the full discussion
See the complete episode of the Soft Robotics Podcast here:
Humanoids daily will continue tracking actuator architectures — and the supply chains behind them — as humanoid prototypes march toward commercial deployments